NanoWEMA®
Forming and welding of ultra-thin-walled tubes
Redefining Precision, Streamlining Processes, Enhancing Quality.
NanoWEMA® is designed for the continuous production of stainless steel microtubes, which serve as precursors for cannulas.
Our advanced NanoWEMA® machines process a variety of metal materials to produce tubes with an outside diameter ranging from Ø2.0 to 6.0 mm and a wall thickness of 0.06 to 0.20 mm.
Technical characteristics
NanoWEMA® | |
---|---|
Welding method* | Laser and TIG |
Welding speed range [m/min] | up to 20 m/min depends on wall thickness and welding power |
Outer diameter [mm] | 2 - 6 |
Wall thickness [mm] | 0.06 - 0.2 |
Typical application | Healthcare, Automotive, HVAC |
*#Laser welding Line for stainless steel micro tubes as pre-material for cannula #Green Laser welding Line for Cu tubes – Heat exchanger applications |

-
Low Power Laser: ideal for precise applications with low energy consumption
-
Laser Safety: Laser beam protection hood, LASER class 1 certified
-
Compact Dimensions: space-saving layout with minimal space requirements
-
Interchangeable Welding Heads: various Laser types tailored to applications
-
Modular design: exchangable components with integrated control cabinets
NanoWEMA® – Mastering the Art of Miniature Welding
NanoWEMA® - High precision manufacturing line for small, thin-walled tubes
NanoWEMA® is designed for continuous production of micro tubes with modular design allowing an easy exchange, omission or addition of single machine equipment, adapted on customers’ needs.
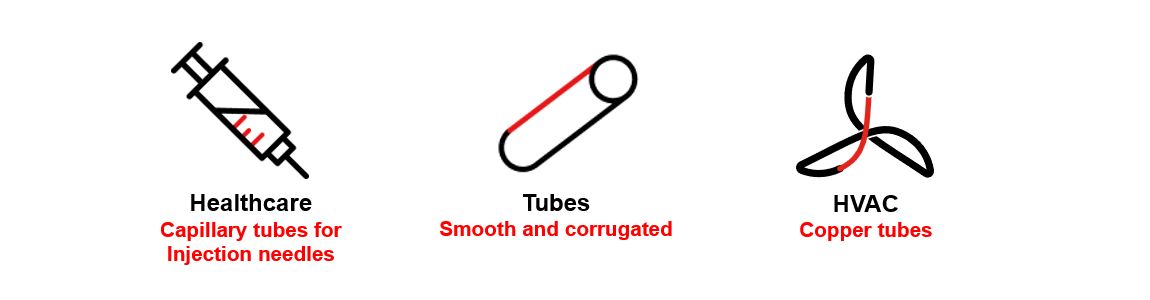
-
Suitable for production of semi-products for cannulas, wire end ferrules, temperature sensors and more
- Cu micro tubes
Industrialized Green laser welding for small copper tubes
applicable for air conditioning units
Key benefits
Our solutions fulfill specific standards you can rely on whilst providing great flexibility.
- Minimized Space Requirements: fewer process steps result in less equipment and a smaller production area
- Automating critical steps reduces the need for manual handling, which in turn decreases labor costs
- Streamlined production processes minimize material waste and enhance operational efficiency
- Optimized process and lifespan: fewer wear-out parts reduce machinery wear, lowering maintenance needs and extending equipment lifespan
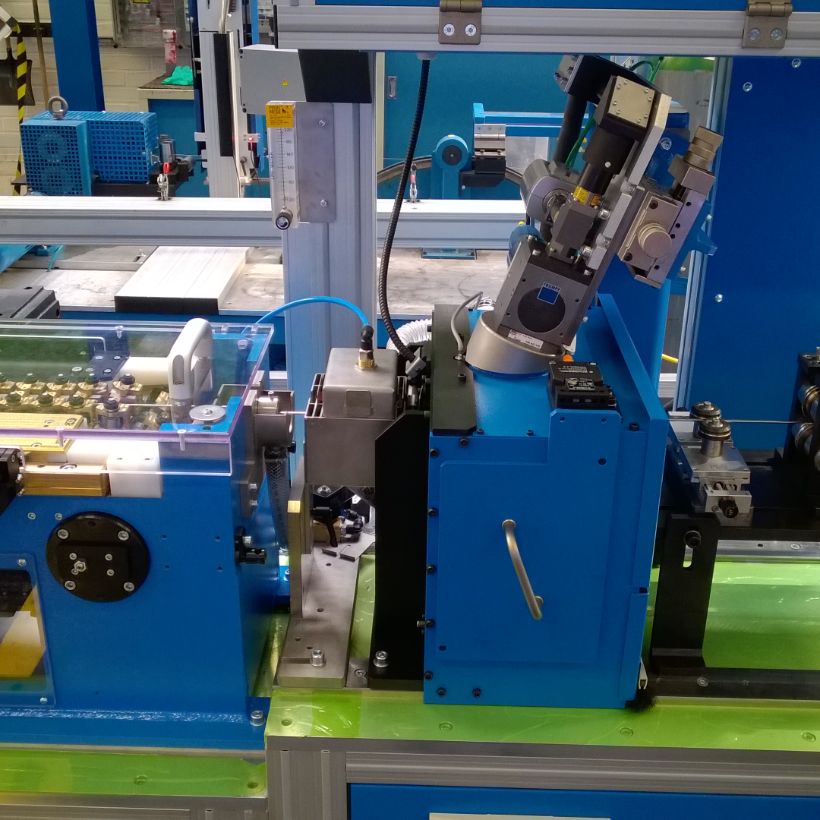
Extended capacity
Capacity increase without further manufacturing space?
Complementary components
Our machine comes in with a series of processing units to ensure complete production lines solutions for continuous manufacturing. Every step of the process is taken care of.
Our additional component portfolio comprises pay-offs, take-ups, taping machines, various forming and reduction tools, different types of belt and caterpillar capstans and many more. For continuous production we provide the necessary solutions, such as cross welding units and accumulators as well as automation concepts.
Processing units
Our websites
Select your country to find our products and solutions
-
Africa
- Africa
- Ghana
- Ivory Coast
- Morocco
- North West Africa
- Americas
- Asia
- Europe
- Oceania