Applications
UniWEMA® solutions designed for the manufacture of cable sheaths, tubes or pipes have found wide use in the industry because of the advantages they provide compared to other production methods. UniWEMA® solutions stand out thanks to exceptional product properties ensuring efficient set-ups whilst allowing for substantial energy and financial savings.
Applications
Covering a wide range of applications
UniWEMA® solutions can help produce a variety of special products, both in the electric/fiber optic cables and in the mechanical tubing and pipe fields, thus achieving optimal desired product characteristics.
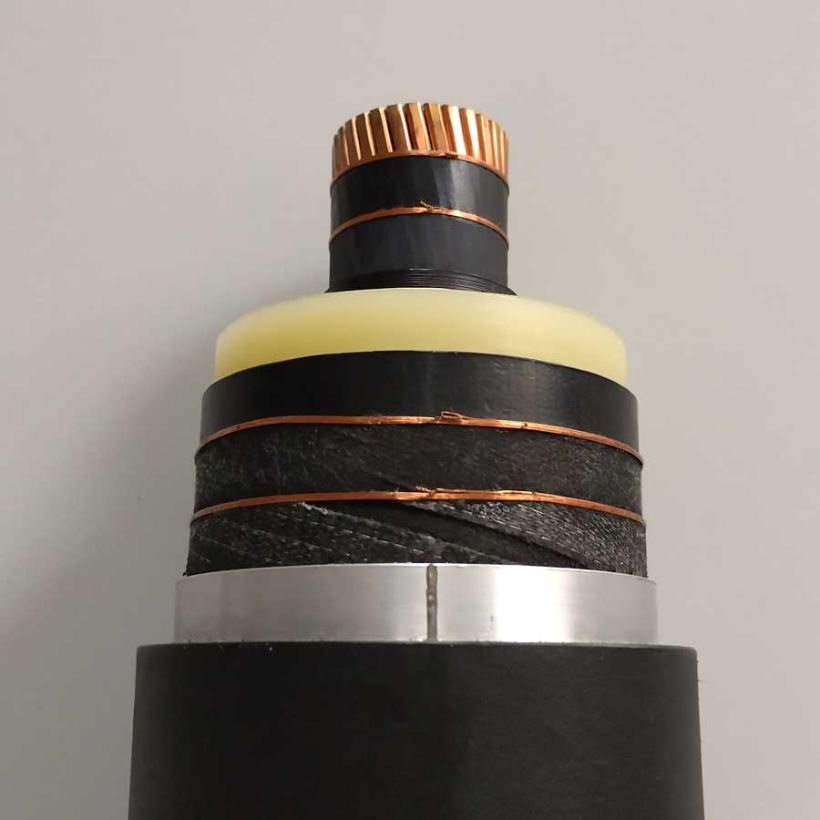
Electricity from renewable energies is one of the core instruments to achieve energy transition. Wind farms need a lot of high voltage and subsea cables to be connected to the grid. UniWEMA® solutions secure a long lasting lifetime of the produced cables with our unmatched know-how in sheathing and cable design:
- high performance cable design
- minimum machine downtime for continuous production of long cable lengths
HTS cables are advanced power transmission solutions designed for LV, MV, and HV applications. These cables must be cooled to 67K using liquid nitrogen (LN₂) to maintain superconducting properties. UniWEMA® MicroWEMA technology plays a crucial role in manufacturing the cryostat, a key component that directly impacts system performance and reliability. MicroWEMA® machines produce the corrugated tubes used in the cryostat, ensuring optimal flow and pressure for the efficient circulation of LN₂, which is essential for sustaining the superconducting effect.
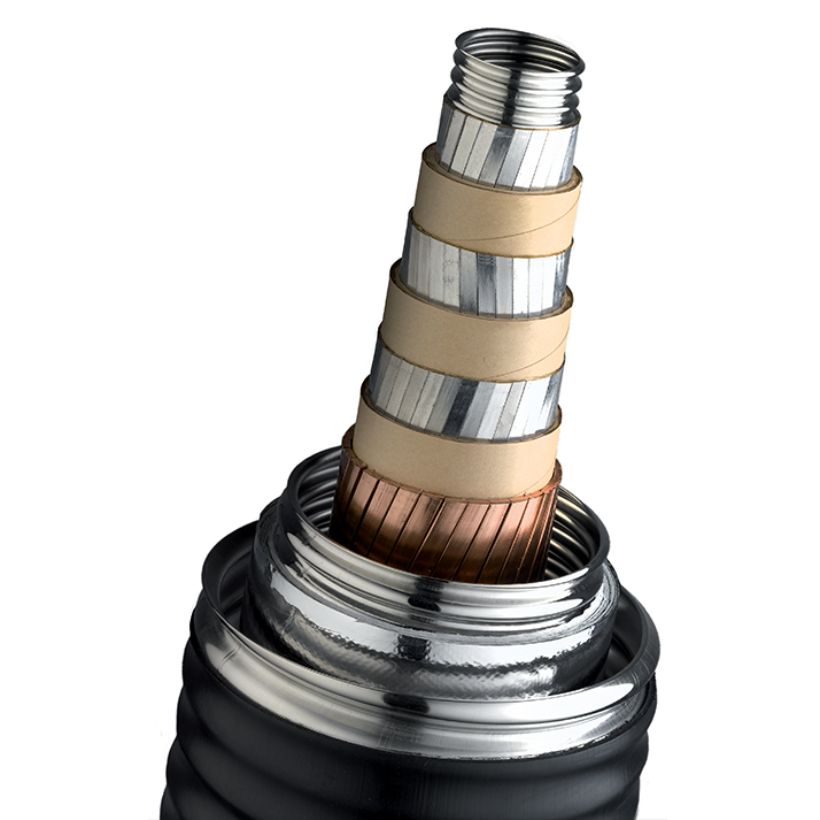

In 2022, more than 30% of the generated energy in Europe is used for heating. Heat pumps play a key part in decarbonizing this sector, since they need only about a third of the energy demand of other electric heating equipment. To ramp up manufacturing capacity and increase the energy efficiency of heat pumps and AC units, UniWEMA® solutions supply the HVAC industry with our know-how in tube design and tube manufacturing.
- increased automation in heat exchanger manufacturing process
- increased heat exchanger energy efficiency
- reduced copper demand, reduced scrap
The world population is growing with 9.7 billion human being expected in 2050. Access to safe and affordable medical supplies will be a paramount. UniWEMA® forming and welding machines allow the manufacturing of injection needles and cannulas with significantly reduced energy consumption, less production steps and reduced material demand.
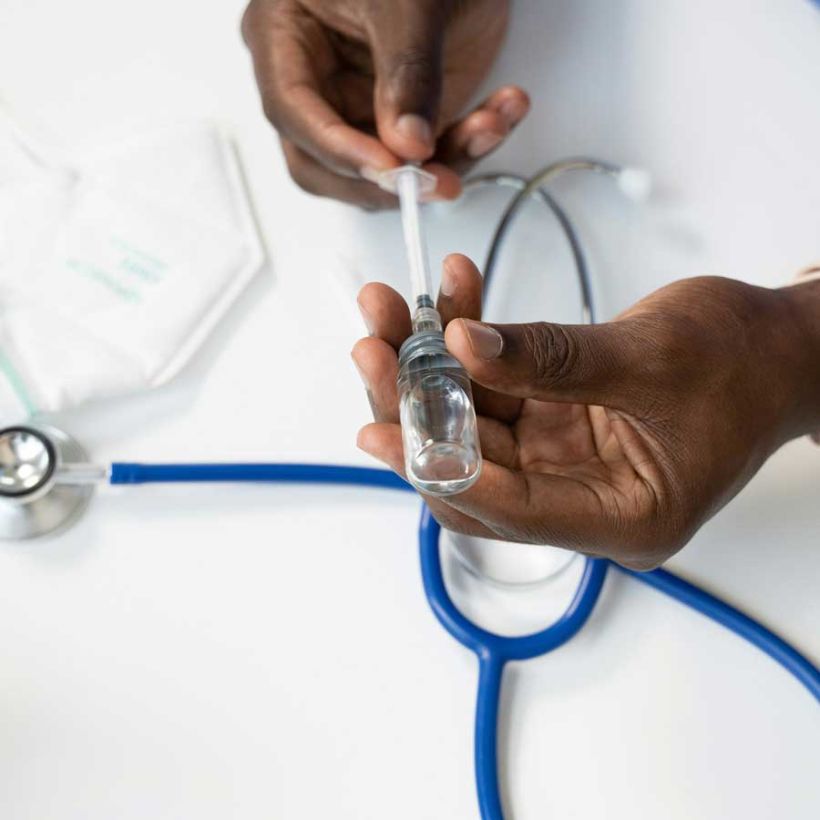
Our websites
Select your country to find our products and solutions
-
Africa
- Africa
- Ghana
- Ivory Coast
- Morocco
- North West Africa
- Americas
- Asia
- Europe
- Oceania