Services and support
Maximizing your productivity with flexible and efficient solutions while minimizing unplanned downtimes thanks to our comprehensive range of services
Machine downtimes can result in significant financial losses.
UniWEMA® service solutions are specifically designed to minimize disruptions to your daily operations. Our remote troubleshooting capabilities and minimal training requirements help maintain the performance of your machines with little impact on your workflow.
Regular maintenance and proactive services not only extend the lifespan of your equipment but also support its long-term health and sustainability.
By ensuring optimal performance, we assist in preventing early obsolescence and enhancing your return on investment.
Comprehensive OEM Services: From On-Site Support to Remote Monitoring
On-site and Off-site support (diagnosis, installation, testing & commissioning, training)
Technical Assistance, remote service and real-time data analytics
Support
Rapid deployment of expert service teams for installation, maintenance, and urgent repairs.
With prompt response times, remote diagnostics, and a proactive maintenance approach, we ensure your machines are operational when required, improving overall productivity and reducing delays in the production process.
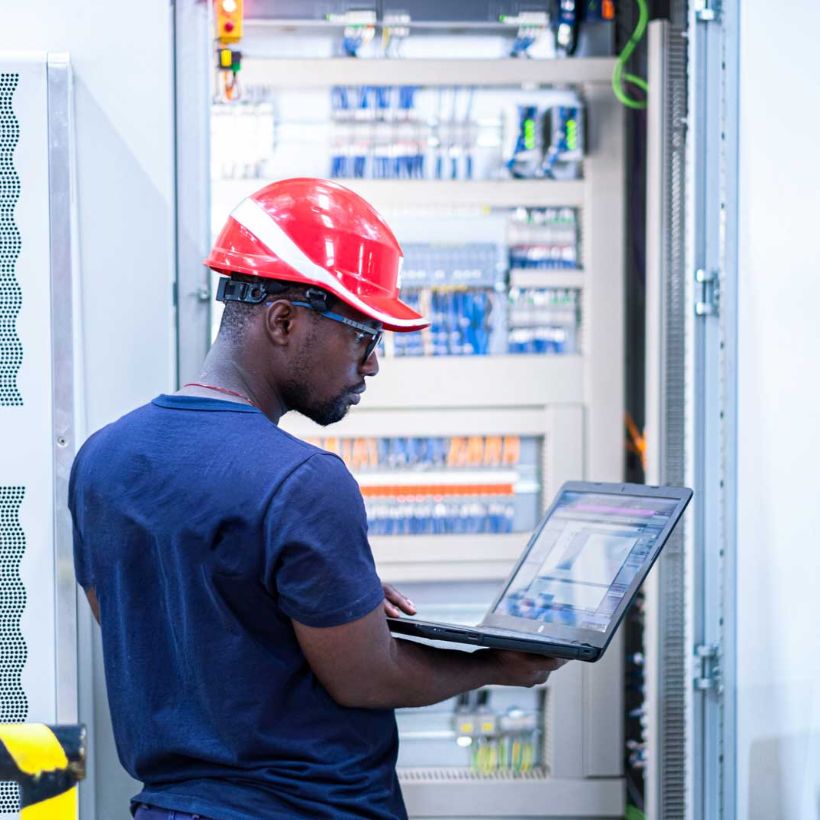
- On-site support : in case of breakdown, our technicians will be on-site within a few days to resolve the issue.
- Remote support: our machines are optionally equipped with remote access, allowing for remote diagnosis and problem solving.
- Flexible spare parts solutions: Relying on targeted procurement and maintaining close collaboration with our suppliers enables us to efficiently source the necessary parts and deliver them directly to your production site.
- Framework agreement for spare parts: customized framework agreements for spare parts ensure faster processing, priority access to critical components at competitive costs, and reduced downtime, simplifying maintenance planning and benefiting all parties.
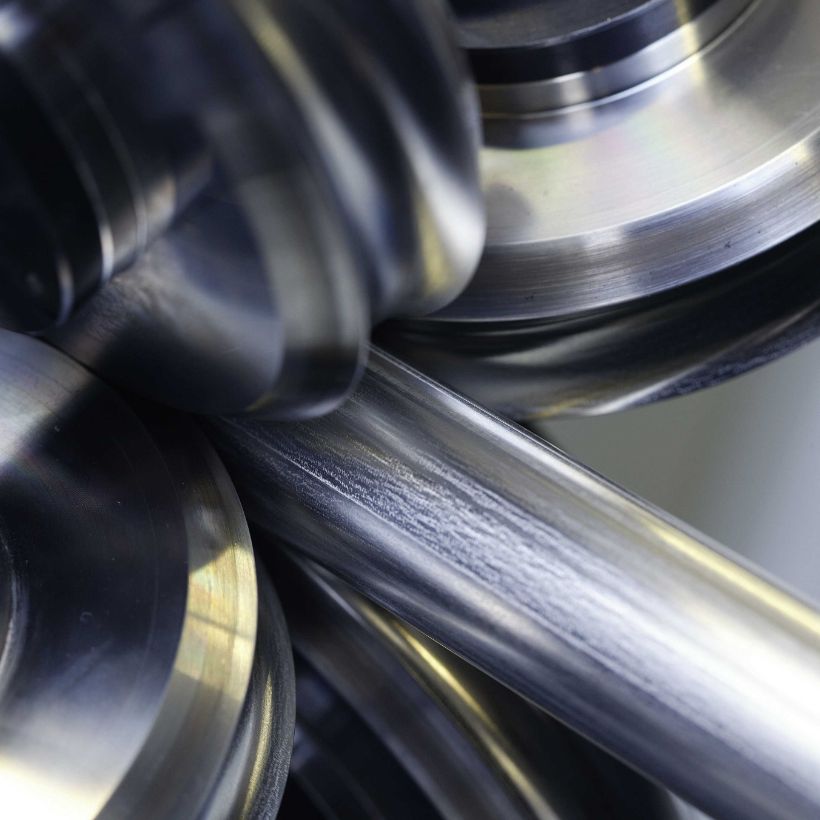
Maintenance
Regular maintenance and proactive service not only extend the lifespan of your equipment but also contribute to its long-term health and sustainability. By ensuring optimal performance, we help you avoid early obsolescence and maximize the return on your investment.
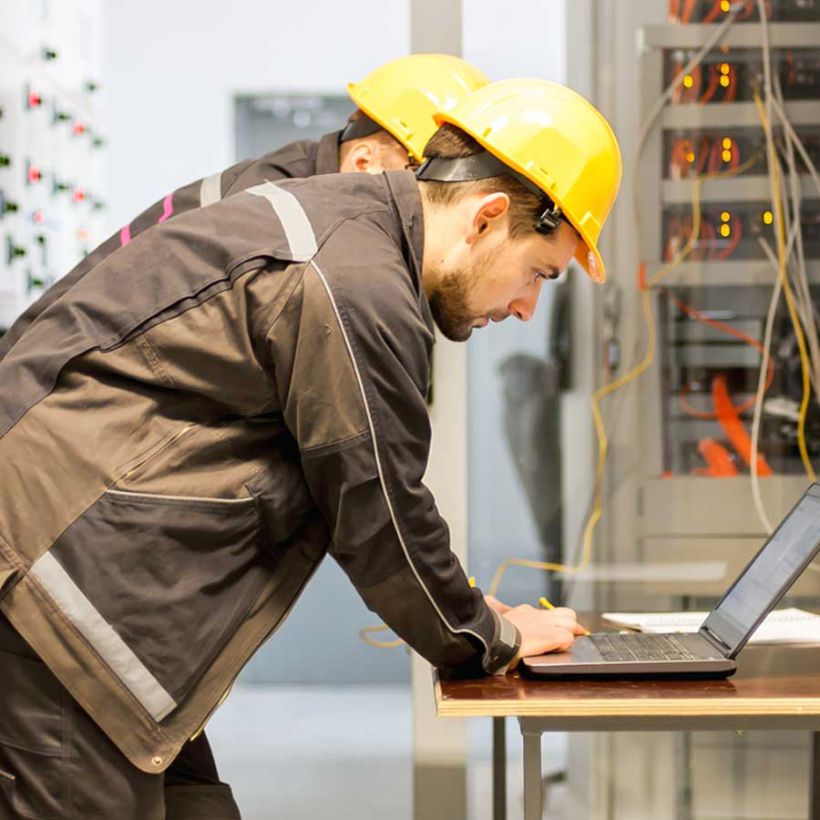
- Contractual agreements for annual maintenance: customized maintenance contracts ensure regular inspections and servicing of your equipment. These agreements provide planning reliability and help extend the lifespan of your machines.
- Proactive support for maintenance teams: by implementing proactive maintenance strategies, we help your team identify and address potential issues early. This reduces unplanned downtimes and optimizes operational efficiency.
Retrofitting operations
As technology advances and requirements change, machines may become outdated. Modernizing existing machines provides a cost-effective and sustainable alternative to investing in new systems.
Our modernization services cater to both our own equipment and third-party machinery. Strategic retrofitting extends the operational lifespan of your equipment, improves its efficiency, and supports sustainability initiatives. Furthermore, upgraded machines can typically be integrated into existing systems with minimal modifications, thereby reducing the need for extensive operator training.
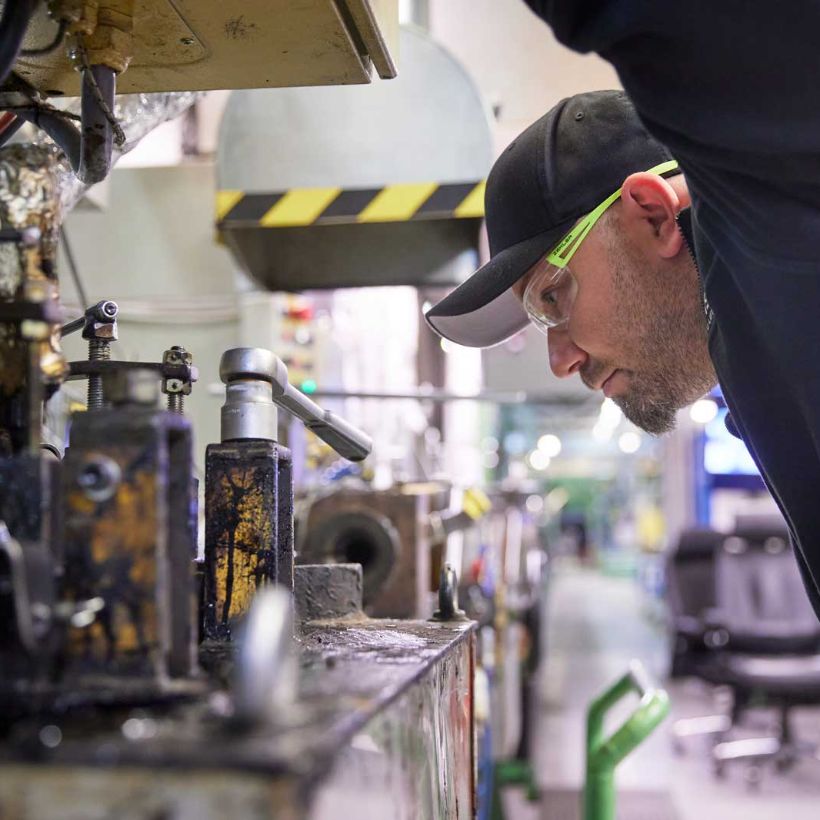
- Integration of new control systems allows for machine upgrades for Industry 4.0 and seamless integration into the operator’s IT environment
- Installation of energy-efficient drives replacing old drive systems leading to increased productivity and reduced energy consumption
- Replacement of outdated components with modern components - when no spare parts available - to ensure operational safety
- Installation of new automation functions enhances efficiency and enables more precise control of production processes
- Integration of new welding technologies into existing systems, including the revision of control systems, leads to increased production, improved weld quality, reduced operating costs and higher energy efficiency
Remote service and real-time data analytics
With remote service and real-time data analytics we predict and diagnose issues before they become critical, reducing downtime and improving efficiency.
Through remote service, we can offer timely assistance, troubleshoot problems, and perform software updates without the need for on-site visits. This not only saves time and costs but also ensures continuity and enhances overall productivity.
-
Increased efficiency: remote monitoring and diagnostics enable quick identification and resolution of issues, reducing downtime and maintaining continuous operation
-
Cost savings: minimizing the need for on-site visits allows to save on travel expenses, labor costs, and reduce the time required to address problems.
-
Predictive maintenance: IoT sensors and real-time data analytics allow for predictive maintenance, preventing failures before they occur and extending the lifespan of our equipment
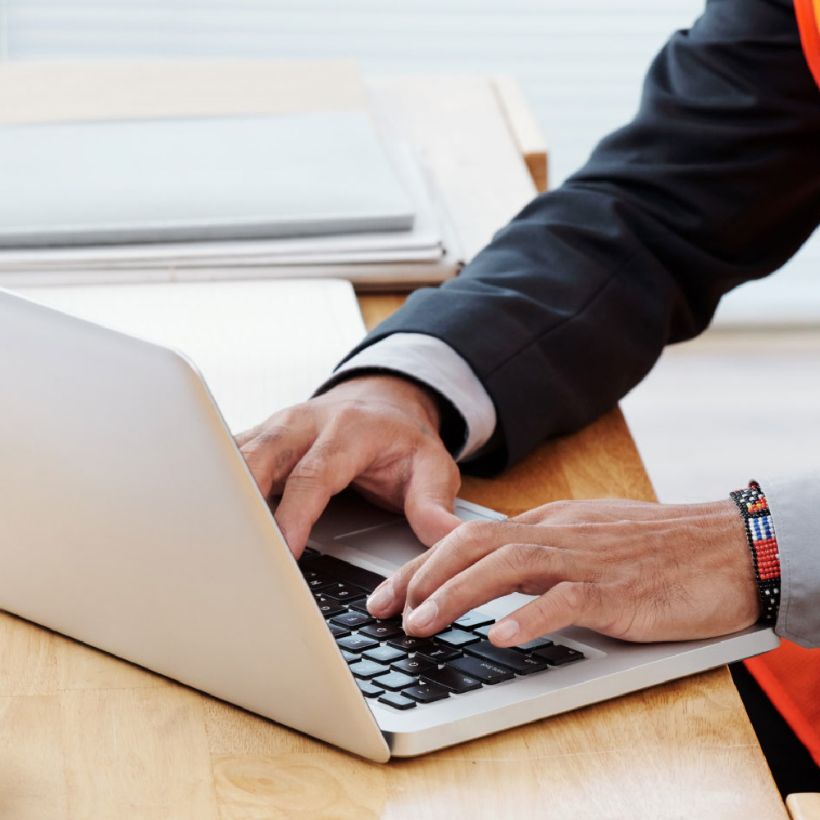
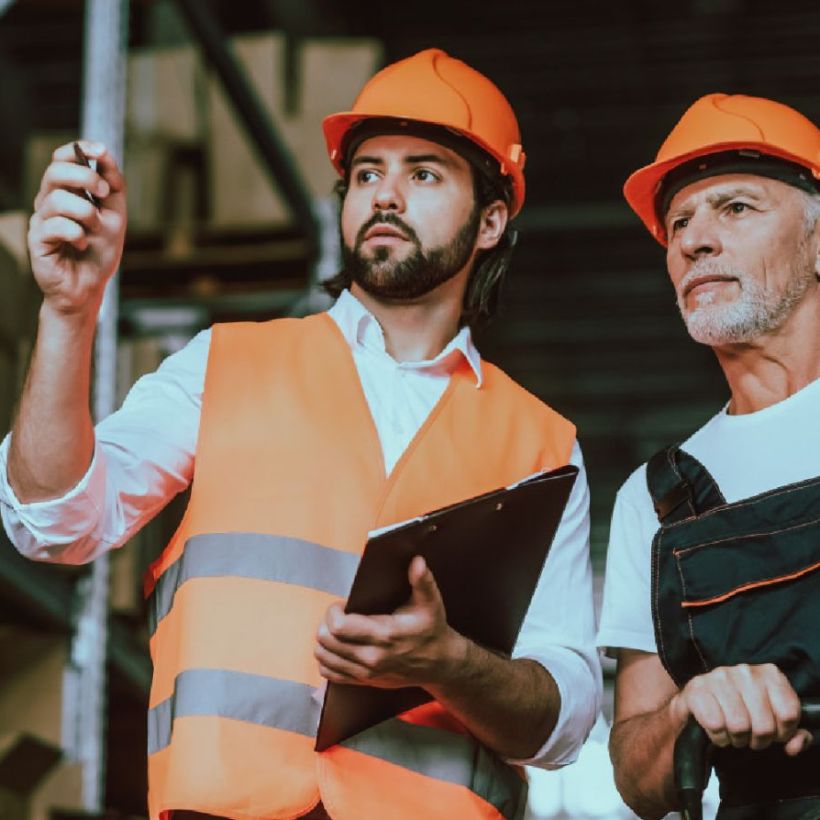
-
Enhanced flexibility: remote service allows to manage and maintain equipment across multiple locations, regardless of geographic barriers
-
Improved safety: remote diagnostics and repairs reduce the need for personnel to work in hazardous environments, which enhance your and our workers' safety.
-
Real-Time support: immediate assistance and support improve service quality and customer satisfaction.
-
Data-Driven Insights: the continuous flow of data from connected machines provides valuable insights for optimizing processes, improving performance, and making informed decisions.
KEY BENEFITS - UniWEMA® services | ||
---|---|---|
Cost effective solutions Save installation time and reduce manual effort |
Our service offering helps you avoid costly machine replacements by optimizing and maintaining existing equipment, providing a more affordable solution than purchasing new machines. Our automation solutions minimize physical labor, reducing manual tasks for operators and improving overall workflow efficiency. |
|
Reduced downtime and increased productivity Optimize inventory management |
Proactive maintenance and quick issue resolution ensure that machines experience less downtime, boosting their availability and reliability. More reliable and efficient systems reduce the need for large inventories allowing you to streamline operations and manage resources more effectively. Modernized systems are designed with components that are easier to source, ensuring spare parts availability and easier maintenance. |
|
Improved performance and greater flexibility React and adapt quickly to market requirements |
Regular maintenance, upgrades, and proactive support ensure that your systems perform at their highest capabilities, enhancing your overall efficiency. Thanks to our remote support and efficient maintenance strategies, you can quickly adapt to market and operational changes, allowing for faster responses to emerging needs. |
Enhanced Revenue Potential through reduced downtime and improved system performance leading to higher revenue generation.
Energy-efficient operations: our focus on energy-efficient upgrades reduces consumption, lowering operational costs and contributing to more sustainable operations.
Our websites
Select your country to find our products and solutions
-
Africa
- Africa
- Ghana
- Ivory Coast
- Morocco
- North West Africa
- Americas
- Asia
- Europe
- Oceania