DeciWEMA®
Forming and welding of smooth and corrugated tubes, cable sheathing, construction pipes
Big performance for big dimensions
DeciWEMA® is used for the production of tubes, cable sheaths and construction pipes made of aluminum, copper, stainless steel and more. It can be equipped with laser or TIG welding technologies for wide range of wall thicknesses. This machine accommodates larger diameters and thicker wall thicknesses, making it perfect for industries requiring high-quality welds on robust materials.
Technical characteristics
DeciWEMA® | |
---|---|
Welding method | High Power Laser, TIG, CathForce |
Welding speed range [m/min] | up to 10 m/min depends on wall thickness and welding power |
Production speed | up to 12 m/min |
Outer diameter [mm] | 50 - 200 |
Wall thickness [mm] | 0.3 - 3.5 |
Typical application | Land and Subsea power cable District heating, Cryogenic transfer lines / envelopes Construction pipes Radio Frequency cable |
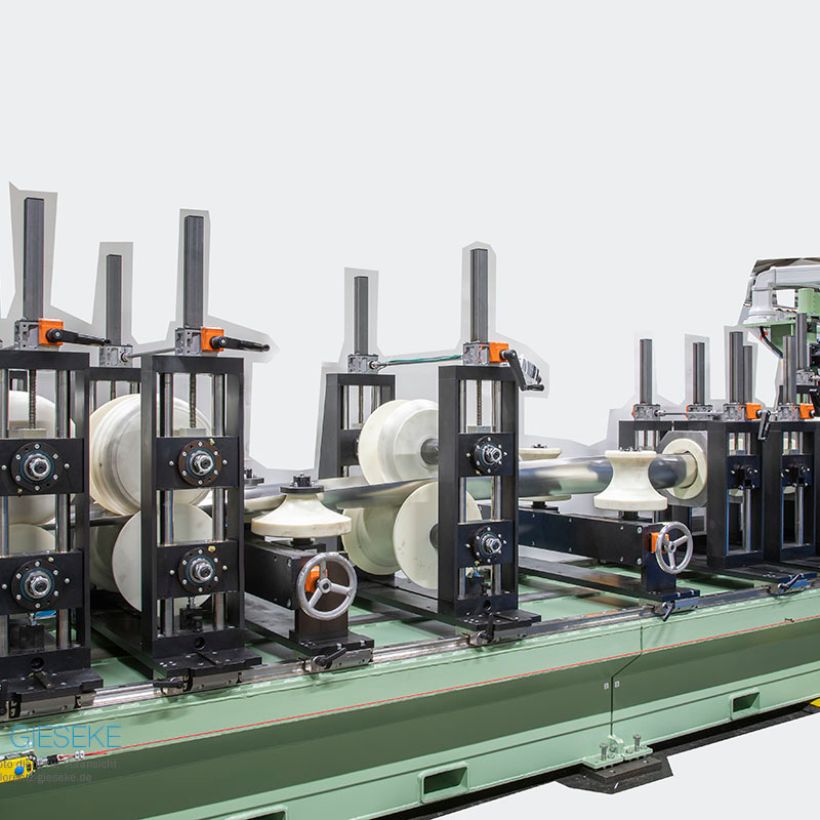
-
Continuous forming and welding of various materials: suitable for aluminum (Al), copper (Cu), steel (ST), and stainless steel (SST)*
-
Interchangeable welding equipment: various high power TIG systems for example Dual-TIG, Polyarc and CathForce
-
Flexible layouts: various configurations available to optimize space usage
-
Easy tool change: user-friendly and recipe controlled
-
Optional: long length manufacturing thanks to accumulator - ideal for various production needs
DeciWEMA® – A Wide Range of Limitless Applications
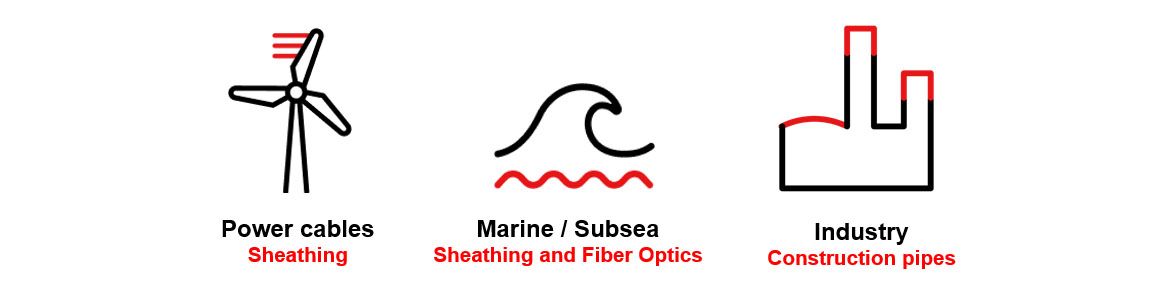
-
Power Cable - DeciWEMA® SAS
Inventor of Laser welding application
Smooth and corrugated Aluminum sheated HV Cable -
Submarine Cable
Replacement of lead
Innovation Laser Welding Application Green/IR -
Application
Smooth and corrugated metal tube
Sheathing of cable cores
Key benefits
Our solutions fulfill specific standards you can rely on whilst providing great flexibility.
-
Optimized process and efficiency: close to zero maintenance downtimes, standardized forming and welding process thus reducing spare part variety
-
Quality: advanced effective recipe management systems ensure constant quality of your production for all different materials
-
Long term reliability (over 50 years lifespan)
-
Industry 4.0. : ready for smart factory integration
- Remote support for parameter adjustment and diagnosis
_rebranded.jpg/jcr:content/DeciWEMA-3-(1)_rebranded.jpg)
Complementary components
Our machine comes in with a series of processing units to ensure complete production lines solutions for continuous manufacturing. Every step of the process is taken care of.
Our additional component portfolio comprises pay-offs, take-ups, taping machines, various forming and reduction tools, different types of belt and caterpillar capstans and many more. For continuous production we provide the necessary solutions, such as cross welding units and accumulators as well as automation concepts.
Processing units
Our websites
Select your country to find our products and solutions
-
Africa
- Africa
- Ghana
- Ivory Coast
- Morocco
- North West Africa
- Americas
- Asia
- Europe
- Oceania