MicroWEMA®
Forming and welding of smooth and corrugated tubes and cable sheathing
Flexibility to the core
MicroWEMA® is used for the production of small tubes and cable sheaths made of aluminum, copper, stainless steel and more. It can be equipped with laser or TIG welding technologies for wide range of wall thicknesses.
Technical characteristics
MicroWEMA® | |
---|---|
Welding method | Laser and TIG |
Welding speed range [m/min] | up to 30 m/min depends on wall thickness and welding power |
Production speed | up to 40 m/min |
Outer diameter [mm] | 2 - 60 |
Wall thickness [mm] | 0.1 - 1 |
Typical application | Subsea Telecom, Sensor cable, Subsea repeater, Overhead lines Radio Frequency Cable, Downhole cable, Railway cable Composite pipes, CSST - Corrugated stainless steel tubes |
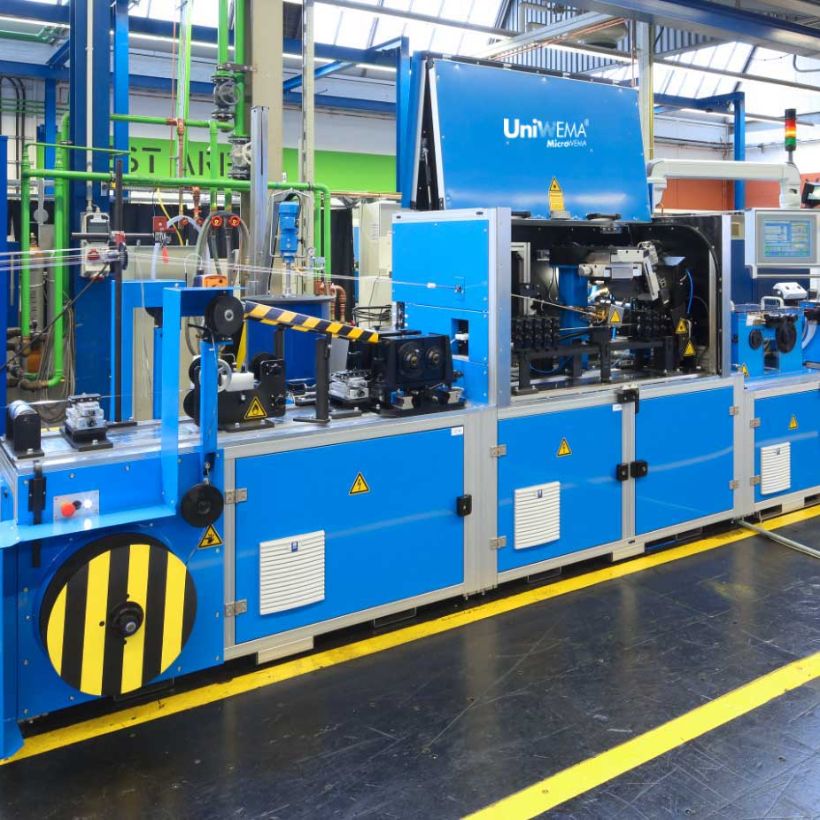
-
Versatile forming and welding options using Laser or TIG welding technologies
-
Continuous forming and welding of various materials: suitable for aluminum (Al), copper (Cu), steel (ST) and stainless steel (SST)
-
Laser Safety: laser beam protection hood, LASER class 1 certified
-
Interchangeable welding equipment: various Laser and TIG types tailored to various applications
-
Modular design: exchangable components with integrated control cabinets
-
Easy tool change: user-friendly and recipe controlled
-
Optional: long length manufacturing (up to 100 km) thanks to multicoil or accumulator - ideal for various production needs
MicroWEMA® – A Wide Range of Limitless Applications
MicroWEMA® solutions are involved in a wide range of applications
- Smooth and corrugated metal tubes
- Sheathing of cable cores
- Optical fibre in stanless steel tubes
That can be used across a whole series of segments and applications.
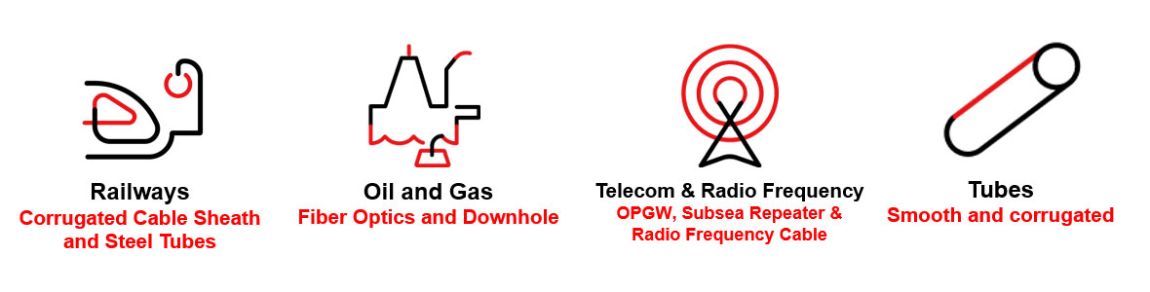
That can be used across a whole series of segments and applications : Subsea Telecom, Sensor cable, Subsea repeater, Overhead lines, Radio Frequency Cable, Downhole cable, Railway cable, Composite pipes, CSST - Corrugated stainless steel tubes for heat exchanger, slider, fiber in steel tubes.
Key benefits
Our solutions fulfill specific standards you can rely on whilst providing great flexibility.
- Increased production efficiency: higher welding speeds are achievable with state-of-the-art laser sources, reducing production time and increasing overall throughput
- Cost and energy savings: the system has an energy efficiency rate of over 70%, which helps lower operational costs and support sustainable manufacturing practices
- Designed for straightforward operation, the system features pre-set recipes and settings that enable operators to use it independently. This reduces the need for extensive training and minimizes errors
- Exceptional reliability and uptime: this system delivers an operational availability of over 95%, ensuring consistent reliability and continuous performance, thus maintaining smooth production with minimal disruptions
- Safety: incorporating built-in safety features, including a Laser Class 1 protection hood, ensures a secure working environment and full compliance with industry safety standards
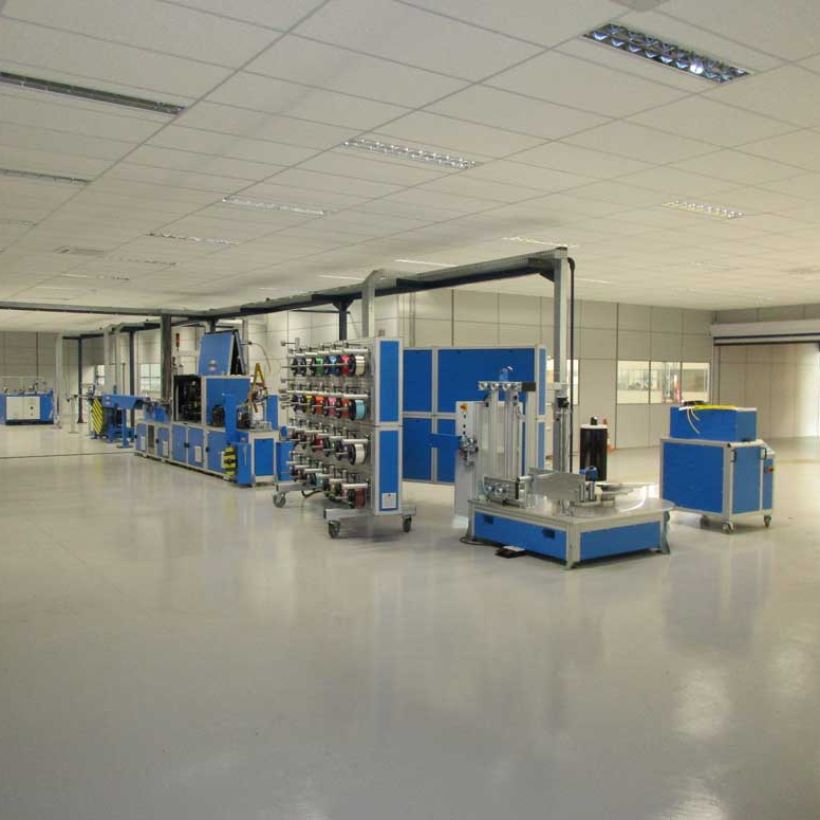
Extended capacity
Capacity increase without further manufacturing space?
Complementary components
Our machine comes in with a series of processing units to ensure complete production lines solutions for continuous manufacturing. Every step of the process is taken care of.
Our additional component portfolio comprises pay-offs, take-ups, taping machines, various forming and reduction tools, different types of belt and caterpillar capstans and many more. For continuous production we provide the necessary solutions, such as cross welding units and accumulators as well as automation concepts.
Processing units
Our websites
Select your country to find our products and solutions
-
Africa
- Africa
- Ghana
- Ivory Coast
- Morocco
- North West Africa
- Americas
- Asia
- Europe
- Oceania